General Fibre Glass Mouldings
As one of the UK’s leading glass fibre moulding manufacturers, you can trust in our attention to detail, dedication and exceptional standards within each and every project we work on.
What We Offer
General FIBRE gLASS mOULDINGS
Explore our varied portfolio of general moulding projects and get a feel for the quality and huge range of our work.
Examples of General Mouldings include:
- Any bespoke mouldings
- Kiosks
- Under water Anode shields
- Bollards
- Planters
- Life Raft Holders
- MOD Seats for ships
- F1 Garage tool boxes
- Medical Boxes
- Overlaying Polystyrene props
- Containers for Water treatment plants
- Security Camera covers
- Remote controlled boats for Environmental agencies
- Theme Park restoration services – Flumes, rock restoration etc
- Leisure Centre slides
- 6m Aircraft refuelling nose cone transportation containers
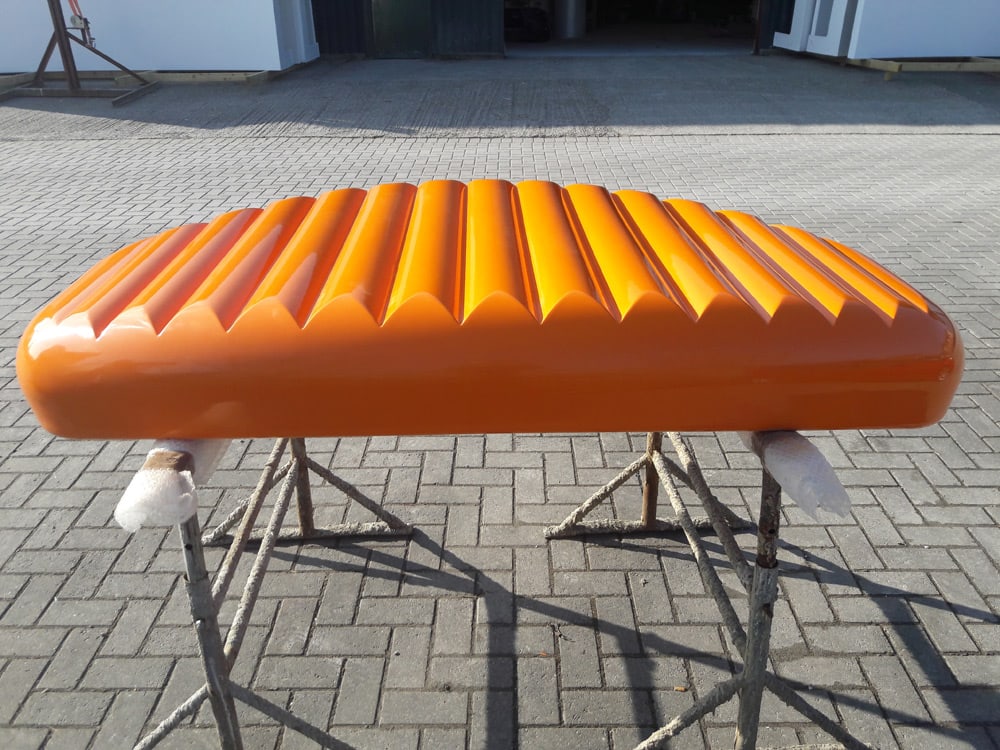
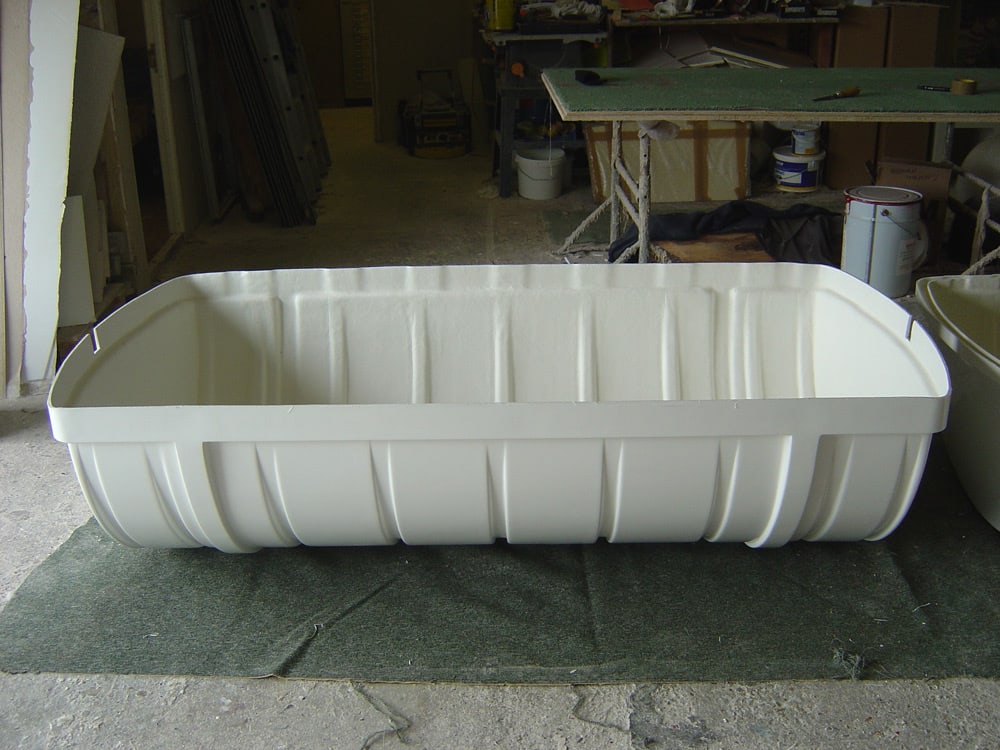
What is Fiberglass Molding?
Fibreglass GRP (Glass Reinforced Plastic) or FRP (Fibre Reinforced Plastic)? All refer to the same thing: a mat or cloth of glass fibres embedded in a plastic resin.
What we call it isn’t that important, but how we make it is, traditionally, fibreglass products are made by coating an open mould with a gel coat. Layers of glass fibres are then built up with plastic resin being manually applied. The result is then left to cure so the resin can harden before the mould can be reused. It’s messy, emits lots of fumes and requires a lot of labour.
Moulds fall into two groups – male and female. Glassfibre is laminated on the outside of a male mould and on the inside of a female mould. The desired finish whether it be smooth or textured will be on the side nearest to the mould so a female mould would be used to produce car body parts, boat hulls etc where the finish has to be on the outside of the mould. A male mould would be used on such things as baths, shower trays etc where the finish has to be on the inside of the mould.
Workshop conditions are important when mould making as temperatures need to be managed between the ranges of 18º– 22ºC, moulds are to be kept out of direct sunlight and any heat from the workshop should be directed away from the work area as even something as subtle as a draft, hot or cold should be avoided at this stage.
The Plug / Master Mould:
To create a mould first we start with a pattern or sometimes called a ‘plug’ which is an exact replica of the finished item. The plug can even be an existing item such as a car panel or canoe etc but infringing copyrights should be taken into account and avoided. Most times though the pattern must be made from scratch. The pattern can actually be created from almost any material as long as it is made from a rigid, accurate and dimensionally stable material set on a solid foundation.
It is also necessary to have a slight taper on the side walls of the pattern so the mould can be removed easily. Usually, a larger mould would need to have a rigid wooden frame covered in hardboard, plywood or MDF, plaster and clay can also be used as long as it is reinforced with wire netting and hessian as toolmakers tend to manufacture from wood.
The surface must be free of any blemishes and smooth. The wood is then sealed with a hard varnish. This mould can then be used to create many exact replicas as needed for the required industry which is why fibreglass moulds are such a popular choice for companies around the world, Fibre Glass Moulds are constantly extensively researched for new and innovative ideas and uses so the industry is ever-evolving and creating more and more uses for this material.
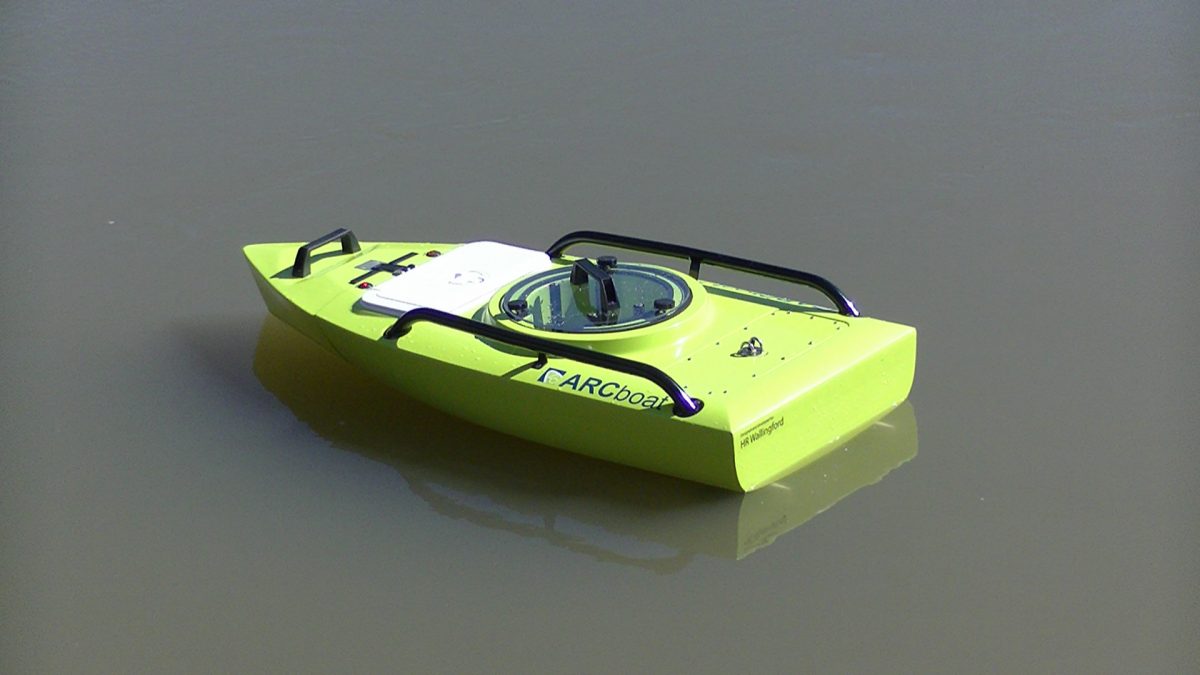
General Fibre Glass Mouldings – Quality & Precision in Every Project
As a leading UK manufacturer of glass fibre mouldings, we take pride in our meticulous attention to detail, commitment to innovation, and the highest standards in every project we undertake.
Whether creating one-off bespoke mouldings or producing complex, high-volume components, we ensure superior quality and durability. Our expertise spans across multiple industries, delivering reliable solutions tailored to unique client needs.
Why Choose Our Fibreglass Moulding Services?
Fibreglass moulding is a highly versatile process used across various industries, from construction and marine to automotive and industrial applications. Our ability to customise every aspect of the moulding process ensures we deliver products that meet the exact specifications and performance requirements of our clients. With state-of-the-art manufacturing facilities and a team of skilled professionals, we offer premium solutions that stand the test of time.
Custom-Built GRP Mouldings for Multiple Applications
Our expertise extends to crafting high-quality, custom-built GRP mouldings for an extensive range of applications. We work closely with our clients to develop solutions tailored to their specific needs, ensuring precise detailing and structural integrity. Our services include:
Architectural & Construction Components: Cornices, columns, cladding, roofing solutions, and bespoke decorative features.
Industrial & Commercial Products: Structural components, access covers, stair treads, gratings, and protective enclosures.
Marine & Automotive Applications: Lightweight yet durable parts such as hulls, decks, car body panels, and aerodynamic elements.
Public & Environmental Sector Solutions: Remote-controlled boats for environmental monitoring, security camera covers, and bollards.
Themed Attraction & Restoration Projects: Theme park restoration services, rock formations, flumes, and bespoke props.
Our Advanced Fibreglass Moulding Process
We follow a structured, high-precision manufacturing process to ensure excellence in every moulding we produce. From initial design consultation to the final product, our approach is guided by precision, efficiency, and durability.
Step 1: Design & Consultation
Our team collaborates with clients to understand their requirements, recommending the best materials and structural features for their mouldings. We use advanced CAD software to create detailed designs, ensuring accuracy from the outset.
Step 2: Pattern (Plug) Creation
The plug, or master mould, serves as the foundation for the final product. We craft it from durable, stable materials to ensure consistency and longevity. The surface is refined and polished to achieve a flawless finish, whether smooth or textured.
Step 3: Mould Development
Using precision techniques, we develop either male or female moulds depending on the required application. This stage is crucial in determining the surface quality and durability of the final product.
Step 4: GRP Lamination & Fabrication
The fibreglass layers are applied to the mould using high-quality resin and reinforcement materials. This process includes careful layering, ensuring strength, flexibility, and resilience against environmental factors such as corrosion, UV exposure, and harsh weather conditions.
Step 5: Curing, Trimming & Finishing
Once the GRP has cured, the moulded product undergoes precision trimming, sanding, and finishing. We can provide a variety of finishes, including textured, smooth, or coloured coatings to suit aesthetic and functional requirements.
Step 6: Quality Assurance & Testing
All products undergo rigorous quality control testing to verify structural integrity, durability, and compliance with industry standards. Our strict quality assurance protocols ensure every product meets the highest levels of performance and safety.
The Benefits of GRP Mouldings
GRP (Glass Reinforced Plastic) mouldings offer a range of advantages that make them the preferred choice for diverse applications:
- Lightweight Yet Strong: Provides excellent strength-to-weight ratio, making handling and installation easier.
- Corrosion & Weather Resistant: GRP withstands extreme weather conditions, chemicals, and environmental exposure without degradation.
- Minimal Maintenance: Unlike traditional materials, GRP requires little to no maintenance over its lifespan.
- Versatile & Customisable: Can be shaped into complex forms and finished in various colours and textures.
- Cost-Effective: Long lifespan and low maintenance requirements provide excellent value for money.
Industry Expertise & Unmatched Customer Support
With years of experience in GRP manufacturing, we have developed a reputation for excellence in craftsmanship, innovation, and customer service. Our dedicated team works closely with every client, providing guidance and support at every stage of the project.
Whether you require a single bespoke moulding or mass production of industrial components, we have the expertise and technology to deliver outstanding results.
Eco-Friendly & Sustainable Manufacturing
We recognise the importance of sustainability in today’s world. Our production process minimises waste, and we utilise eco-friendly resins and materials wherever possible.
By prioritising efficiency and environmental responsibility, we aim to reduce our ecological footprint while maintaining the highest standards of quality.
Get a Free Quote Today!
If you’re looking for expertly crafted fibreglass mouldings that offer superior performance and longevity, look no further.
Whether you need architectural components, marine and automotive parts, or industrial solutions, we can bring your vision to life. Contact us today to discuss your requirements and request a free, no-obligation quote.
1. What is GRP, and why is it widely used?
GRP (Glass Reinforced Plastic) is a composite material known for its strength, durability, and lightweight properties. It is used across various industries due to its resistance to corrosion, chemicals, and harsh weather conditions, making it an ideal alternative to traditional materials such as wood and metal.
What are the benefits of GRP mouldings?
GRP mouldings provide several advantages over traditional materials like wood, metal, or concrete:
- Lightweight: Easier to handle and install.
- Corrosion & Weather-Resistant: Does not rust, rot, or degrade over time.
- Low Maintenance: Requires little upkeep compared to wood or metal.
- Cost-Effective: Long lifespan reduces replacement and maintenance costs.
- Customisable: Available in various shapes, sizes, and colours.
What types of GRP products do you manufacture?
We manufacture a wide range of GRP mouldings and products, including:
- Roofing & Cladding – GRP panels, trims, and flashings.
- Structural Applications – Staircases, balustrades, and walkways.
- Marine & Automotive Components – Boat decks, car body panels, and interior fittings.
- Decorative & Architectural Features – GRP columns, pillars, window surrounds, and canopies.
Can you create custom GRP mouldings?
Yes! We specialise in bespoke GRP mouldings tailored to your exact specifications. Whether you need a unique design, an existing mould replicated, or a completely new custom solution, we can produce high-quality, precision-engineered GRP products to match your needs.
How long do GRP mouldings last?
GRP mouldings are highly durable and can last several decades with minimal maintenance. Unlike wood, which can rot, or metal, which can rust, GRP remains strong, weather-resistant, and stable over time, making it a long-term investment.
Are GRP mouldings easy to install?
Yes! GRP mouldings are designed to be lightweight and easy to handle, making installation straightforward. Many products can be fitted using standard tools, and we provide guidance to ensure a smooth installation process.
What maintenance is required for GRP mouldings?
GRP mouldings require minimal maintenance. They can be cleaned with mild soap and water to remove dirt or grime. Unlike metal or wood, GRP does not need repainting, sealing, or rust-proofing, making it a hassle-free option.
How do you ensure the quality of your GRP products?
We use high-quality materials and advanced manufacturing techniques to produce durable GRP mouldings. Every product undergoes rigorous quality control checks, including strength testing and durability assessments, to ensure they meet industry standards.
What is the lead time for GRP orders?
Lead times depend on the size and complexity of the order. Standard GRP mouldings may be available quickly, while custom designs require additional time for production and finishing. We always strive to complete projects efficiently and on schedule.
How can I get a quote for my project?
You can contact us via our website, email, or phone to discuss your requirements. We offer a free, no-obligation quote, ensuring you get a competitive price for your GRP moulding project.